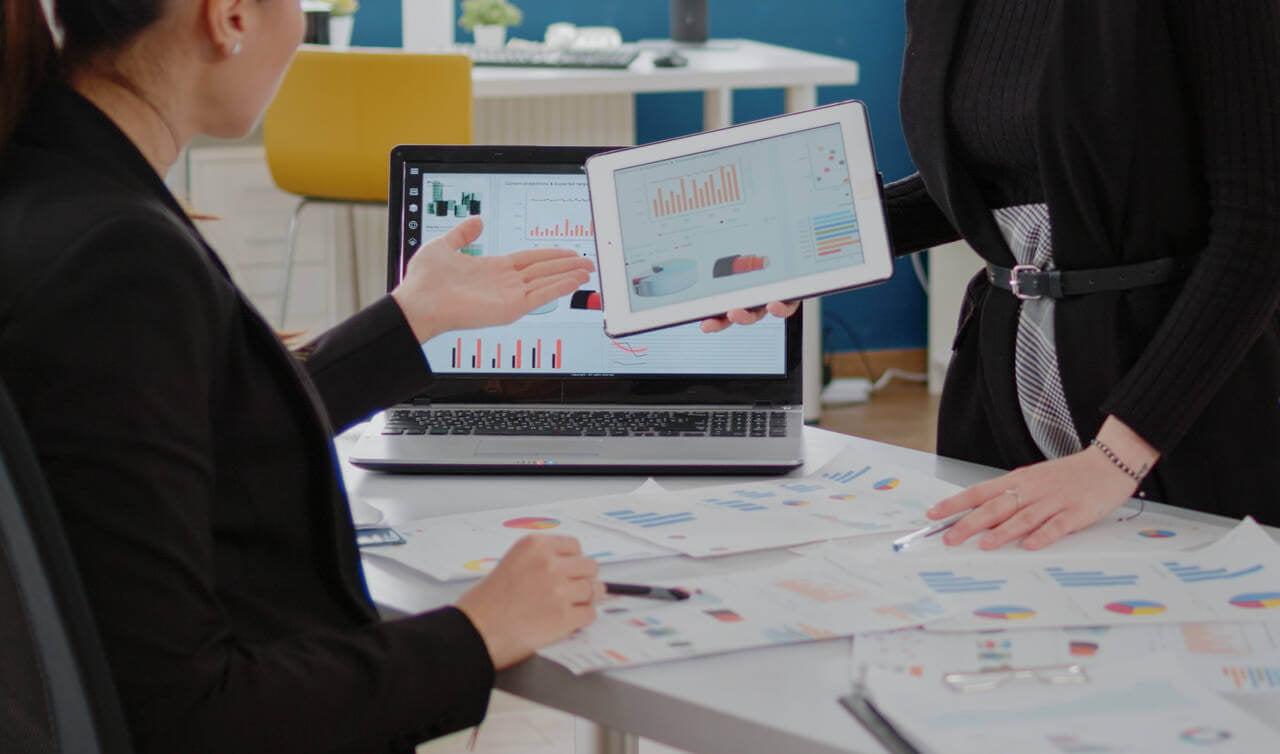
Six Sigma has become a key competence that enables knowledge-based companies to support businesses in achieving specific goals. While you are preparing to start a business or looking for ways to strengthen an existing business, it is worth exploring and considering the benefits of this quality improvement concept. Companies that recognize this phenomenon can optimize their processes for the best possible results. Six Sigma is not only about solving problems based on data, but also about the quality of the data itself.
What Is Six Sigma?
What Is Six Sigma?
Six Sigma is a modern method that aims to improve the efficiency and effectiveness of business processes. It also helps improve profits and growth.
It focuses heavily on measurement, data collection, and statistics. It is not a group that aims at process improvement or optimization, but at improving the quality and efficiency of processes. It can be used in a wide range of industries, even in the original production sector, such as manufacturing equipment, as well as in other sectors. The principle is that by measuring the computing power of a product or service, it is possible to avoid errors, eliminate bottlenecks and find solutions to fundamental problems in the process.
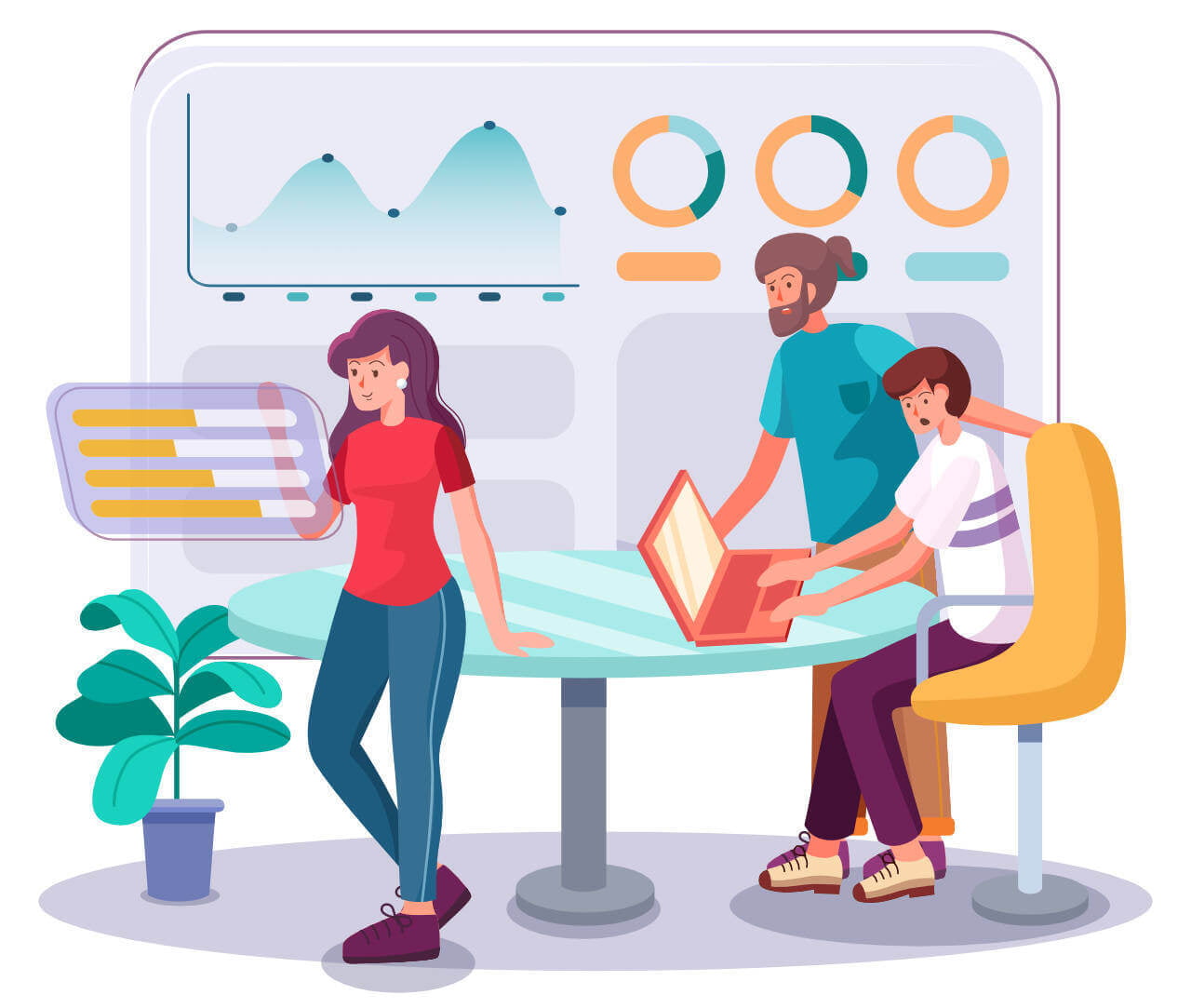
Six Sigma Performance
Six Sigma Performance
Six Sigma is one of the most important factors for the long-term financial success of a company. It is defined as the performance of a process that achieves the best possible results in terms of quality, efficiency, reliability, and cost-effectiveness.
The Greek sigma symbol is a common measure of variation and is used to represent the standard deviation of a group. The practical idea is that if a process can contain only a small number of variables (e.g. a single variable or a set of values), it has a higher probability of producing results than the specification of the result. Most processes cannot sustain a Six Sigma state, but there is a statistical significance for Six Sigma.
The focus is on improving the quality and efficiency of existing processes that have not yet reached their usual optimum conditions and ensuring that new proposals are implemented with a minimum risk of error.
Six Sigma Problem Solution Methodology
Six Sigma Problem Solution Methodology
Six Sigma is not the solution to every business problem you have had for months; however, it is a proven method to improve your operations. Six Sigma is perceived as a ground-breaking method, similar to the way highly qualified martial arts experts use various techniques in their training and practice sessions.
Six Sigma Problem Solution Methodology was originally conceived by Bill Smith of Motorola and later introduced by Mikel Harry in the early 1980s. This groundbreaking work contributed to the development of the successful formula Six Sigma, which uses well-known statistical tools and methods. Six Sigma's strength lies in its ability to consistently apply the methodology to improve a company's ability to predict expected processing performance. In recent years, many of the world's leading companies have used this methodology to increase their profits.
Now let’s delve into the concept of Six Sigma methodology and how to apply it to your company’s benefits.
How Six Sigma Helps Businesses
How Six Sigma Helps Businesses
Business processes and strategies might be carefully constructed and expected to have long-term effects; however, they need to be improved to adapt to the changes that are the need of the hour. Utilizing The Six Sigma method, you can change or improve almost every business strategy or process that goes into operating your business.
Businesses can consistently use the six sigma methodology to achieve goals that optimize shareholder value and lead to satisfied customers. The goal is to optimally balance the cost and quality of the delivery and ensure it fits with the business goals and objectives.
Small and medium-sized enterprises are particularly sensitive to defective parts and services; however, small enterprises also face the same problems as large enterprises in terms of quality and customer satisfaction. Smaller companies are also exposed to Six Sigma's entrepreneurial risk. While larger companies might be able to overcome some shortcomings, they can easily destroy a small company's reputation or customer base. Six Sigma's business risks are similar to those of any other business process, such as human resources, marketing, sales, and operations.
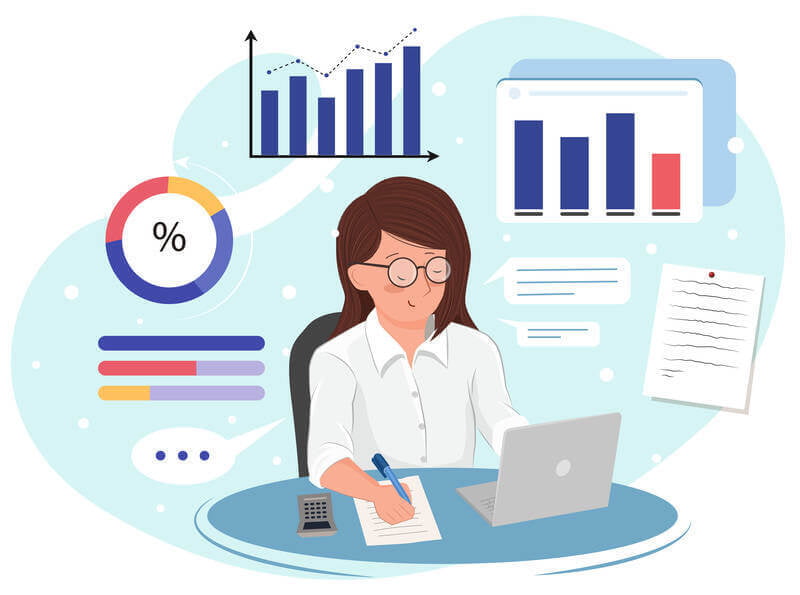
As an entrepreneur, the first step is to make sure your leaders and managers understand that your business needs to perform better, and for that, it requires their support and supervision. . Then you can start your Six Sigma journey based on your Six Sigma goals. This journey also boosts the profit of your company and helps it grow by achieving its goals. Remember that your strategic focus should not be solely on improving profit or growth, but on making the Six Sigma method your business path, exceeding customer expectations, and exceeding your goal. Identify a team of six Sigma consultants who will help you with this. When Six Sigma is well used, it can become part of your company's DNA, not just as a business strategy, but as an integral part of the company. Numerous qualitative and business benefits also have an impact on customer satisfaction, such as better customer service, product quality, and more efficient business processes.
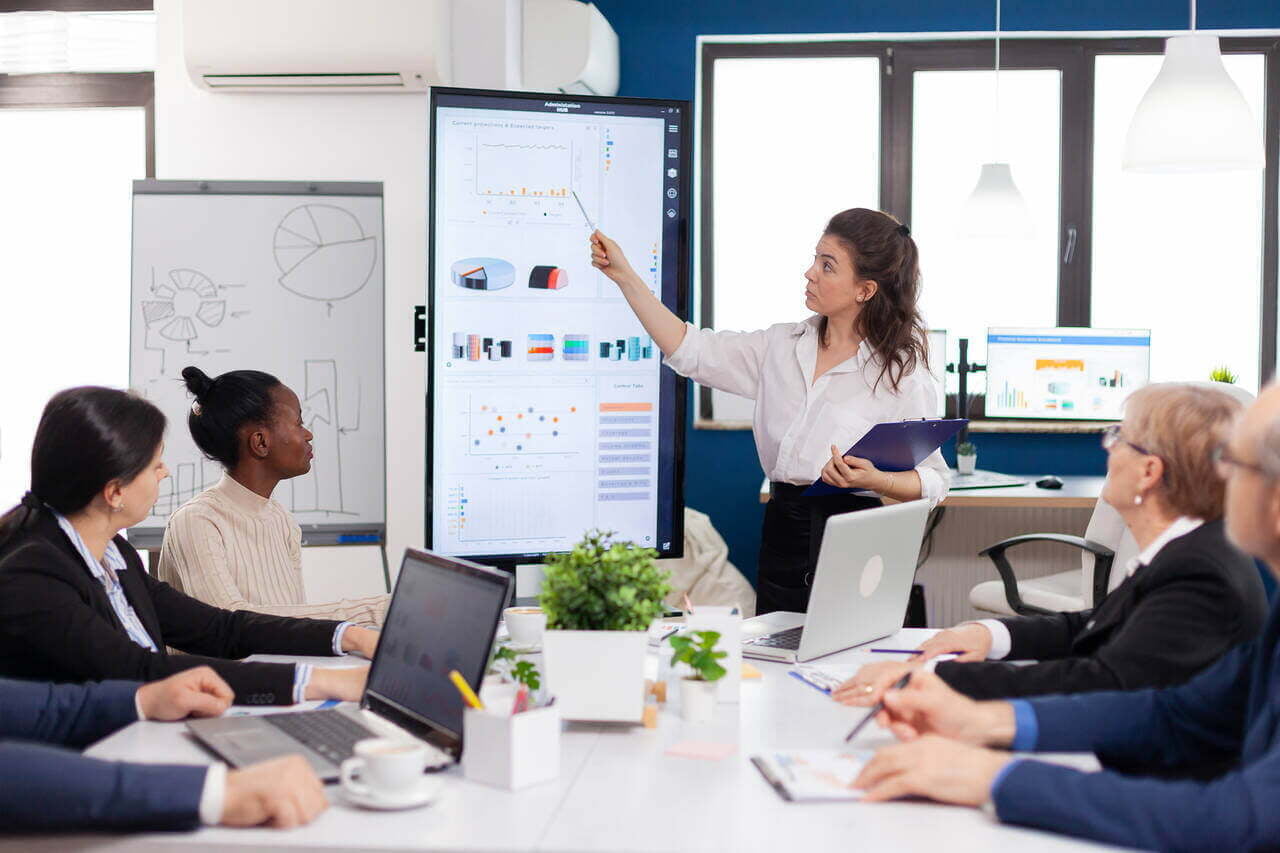
Now that you are familiar with the concept of Six Sigma, let us learn how we apply the Six Sigma methods.
- First, you have to determine which business processes need to be improved and what needs to be done to bring about the required change.
- Once we have identified these needs, a deployment strategy will be developed.
- The next step is to link the goals and objectives of your company to measure performance, goals, and indicators where they are needed.
- Create a balanced scorecard that links business processes with strategic direction, and use a Six Sigma consulting team to help with implementation. A bad bet usually leads to a bad performance, but a good bet leads to a positive result for the customer.
- The next step is to conduct a self-assessment to determine whether the business infrastructure allows the process required to establish a baseline of current performance. We define the performance expected by the customer and create or change new key figures, targets, and specifications if necessary.
- Conduct Six Sigma training, developing internal resources for training, and ensuring that methodology becomes part of your business plan to maintain profit and reduce costs.
Six Sigma Methodology
Six Sigma Methodology
Six Sigma (DMAIC) is a method by which a process can be perfected or, in other words, fine-tuned. DMAIC stands for Define, Measure, Analyze, Improve, and Control. It refers to the step-by-step process of business improvement.
Six Sigma goes beyond that and works to exceed both needs and expectations, working with other aspects of the business, such as quality control, safety, and quality assurance.
- Process optimization is essential. Why, you ask? Let’s find out the answer. Identify and define the cause of the problem, internally or externally, and improve processing performance by addressing or eliminating the cause. Determine the crux of the problem, and take control of the improved process and future process performance.
- There must be a number of defects to achieve Six Sigma. It is important to meet customers' needs as soon as you realize they are there. When transferring to another business unit, the process must have sufficient deficiencies to achieve the objective.
- Wherever our products and services are, Six Sigma DMAIC allows us to achieve near-zero defects. With the improvement that results from the measurement, our product or service can upgrade and remain great.
- Six Sigma (DMAIC) improvements that are integrated into existing processes and do not arise from them are subjected to the standard and require quality control.
- Everything a business does must add value for its customers. Excellent customer service is the way to attract and retain customers. If you do not optimize your process or are far from it, you have to create added value
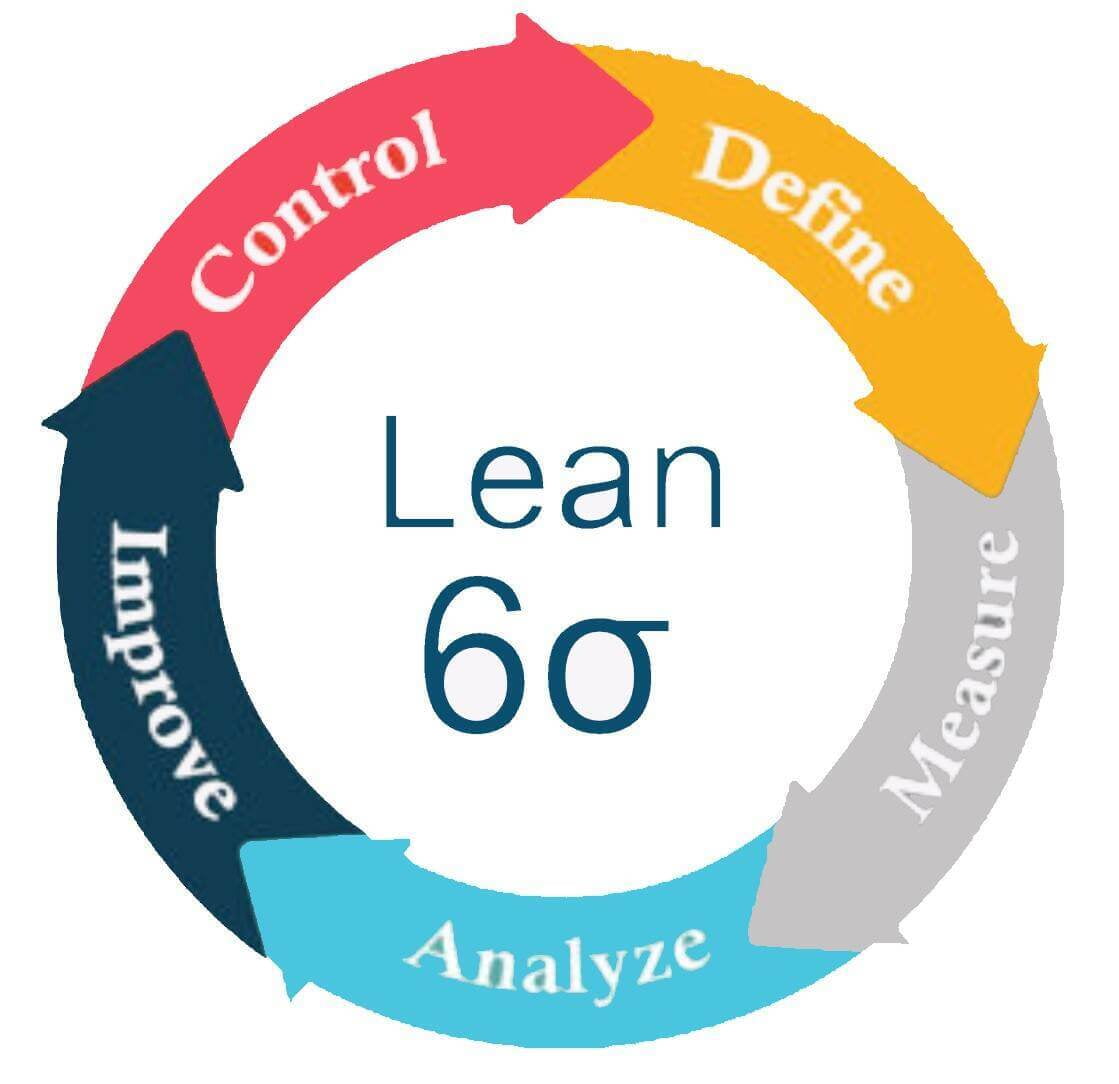